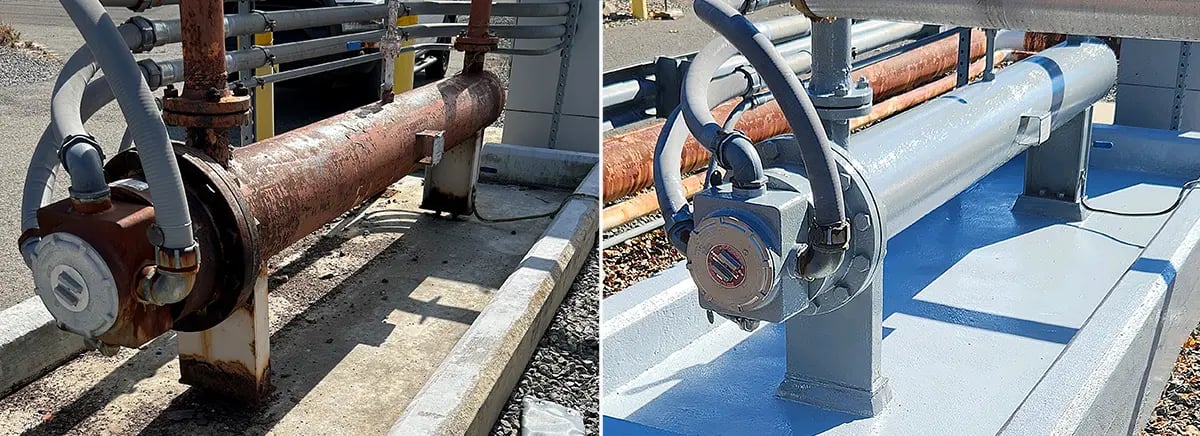
Restoration of Corroded Cylinders Minimizes Risk of Power Plant Outage
Location:
Northern New Jersey power peaking plant.
Pain Point:
After enduring years of service, four fuel oil heater cylinders utilized in cold weather conditions had developed extensive corrosion under insulation, resulting in the possibility of oil leaks and unplanned outage.
Power Peaking Plant's Mission:
Deliver a dependable supply of extra electrical power when demand spikes.
Plant’s Challenge:
Mitigate the risk of an environmental disaster and safeguard against financial losses caused by an unforeseen plant outage. Secure extra time until a complete replacement during scheduled downtime.
The Challenge’s Impact On Day-to-Day Peaking Operation:
The heating cylinders are essential for the power generation process, housing fuel oil heating elements to warm the fuel during cold weather. This facilitates the smooth flow of oil to boilers, where it turns into heat, generating steam that drives turbines for electricity. However, if these cylinders break, it could lead to oil leakage, causing environmental contamination and requiring an unplanned shutdown of the power generation equipment. The integrity of the heating cylinders is crucial for system reliability and environmental protection.
BIG Solution: Restore, Rebuild & Protect With Belzona Coatings
Corrosion under insulation (CUI) often goes unnoticed until it's too late. Fortunately, BIG technicians detected and repaired this CUI situation before it escalated into a major issue.
Over the course of three days, BIG carried out meticulous surface preparation to prevent further damage to the metal substrate. We then applied specialized primers and the surface tolerant Belzona 5831ST coating to repair and protect the corroded cylinders. This coating displaces surface contaminants, ensuring exceptional adhesion even on damp, wet, or oily surfaces. The product also provides long-term corrosion, erosion, and environmental attack protection. To further safeguard against corrosion in wet conditions and future leaks in the insulation jacket, we applied a top coat of Belzona 5811.
In addition to the corroded cylinders, some of the shut-off nozzles had developed holes and were starting to leak. To remedy the corrosion and restore the pipe wall strength, BIG utilized the ASME-compliant Belzona SuperWrap 2 composite repair system.
The Belzona materials used remediate against future corrosion under insulation damage, and also extend the service life of equipment. They are VOC free and completely safe to use, eliminating the need for any hot work during application. These materials cure within hours, allowing for a swift return to service.
The cost of this repair was well below $20k, and the work was completed prior to the fuel oil heater cylinders being put to use in cold weather conditions. Had the CUI issue gone undetected, it could have resulted in an unplanned outage costing millions of dollars per day in lost power generation.
These repairs prepared the plant for winter power peaking. The plant also bought ample time to procure new fuel oil heater cylinders and schedule any necessary replacement work during a planned outage, ensuring that operation and revenue are not negatively impacted.
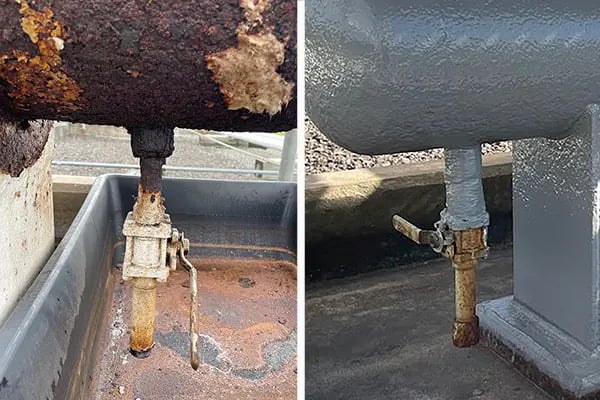
Before and after photo showing corroded valve nozzle and Belzona SuperWrap repair under protective coating.
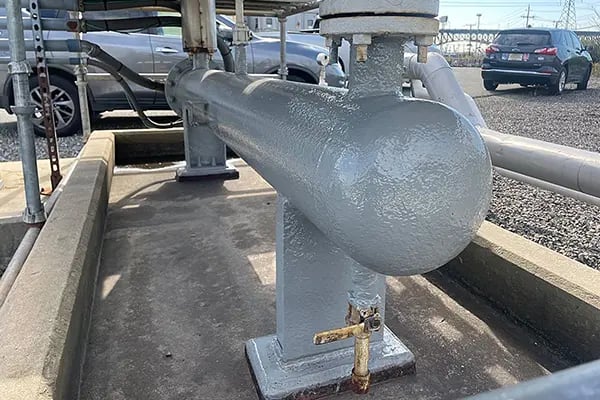
Belzona 5831ST and 5811 protective coatings were used to repair CUI damage to the fuel oil heater cylinders.
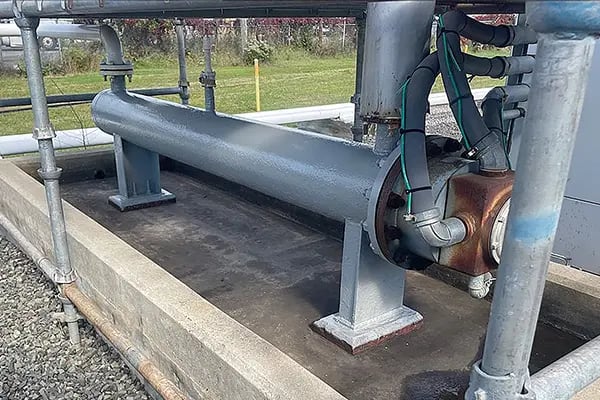
Surface preparation and coating application for four cylinders was completed in just a few days.
For more information about our corrosion under insulation service, and other industrial solutions, contact our team today by calling 856-687-2227.