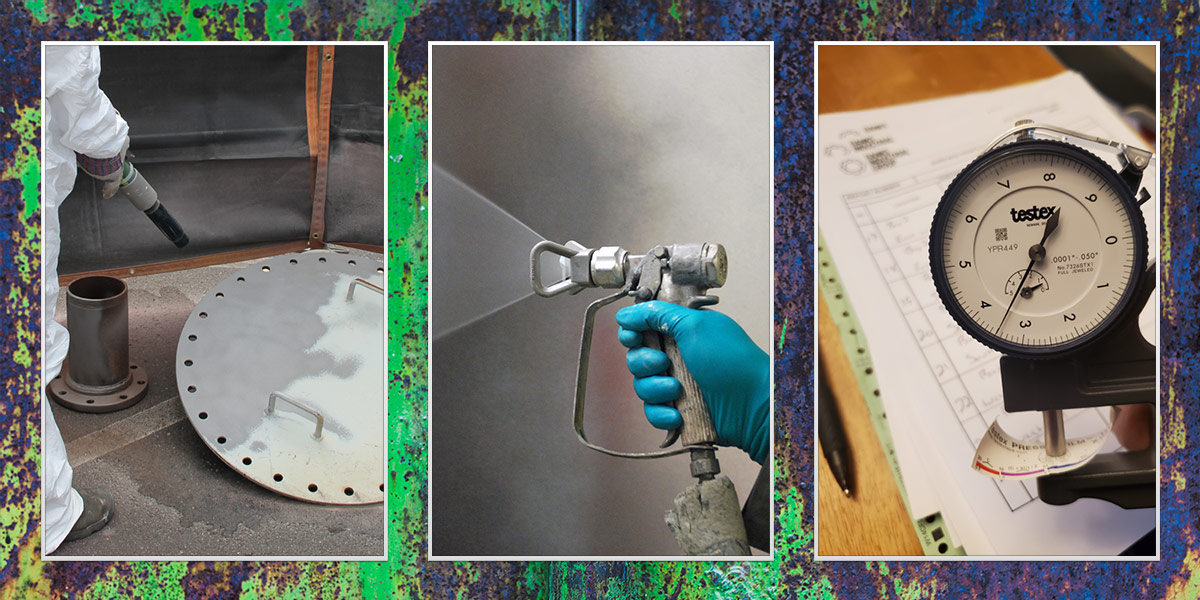
Contents
You’ve no doubt heard the old adage “an ounce of prevention is worth a pound of cure”? In the world of industrial coatings, truer words were never spoken! The right coatings can repair, protect or improve nearly anything made of metal, concrete or rubber provided the most critical components are also mixed in; proper planning, preparation, application, and storage.
Critical mistakes in any of these four stages can cause coatings to fail well before their time. Awareness of potential pitfalls can help you avoid them and extend the longevity of your processes.
The Four Stages of Optimal Coating Application:
1. Preliminary Planning:
The integrity of your coating application begins with step one. During planning, an engineer or coatings expert evaluates the surfaces, or substrate, in need of protection. Any properly developed plan includes pre-application tasks, product selection, and post-application review. Coating failure is often linked back to improper assessment of the substrate.
In selecting the right coating, the evaluator must answer the following questions:
- What is the substrate’s operational temperature?
- Does the temperature ever spike or dip during operation?
- Does the substrate hold any liquids or materials that might interact with the make – Is the substrate cleaned with chemicals that could be harmful to the prospective coating?
- Are we applying a coating to repair or protect the substrate?
While evaluating the substrate, it is important for both parties to agree on a thorough and honest assessment of the substrate’s quality and salvageability. With porous surfaces like concrete, sometimes the concrete or block can be so polluted with salts or chemicals that the best-case scenario for coatings repairs may be less than ideal. To avoid unhappy results, the owner and coatings expert need to communicate about the range of possible results.
After evaluation of the substrate, a coatings expert will select the best coating for the job. Given the potential physical and economic impact of a wrong coating, it’s imperative that you have a knowledgeable and experienced source.
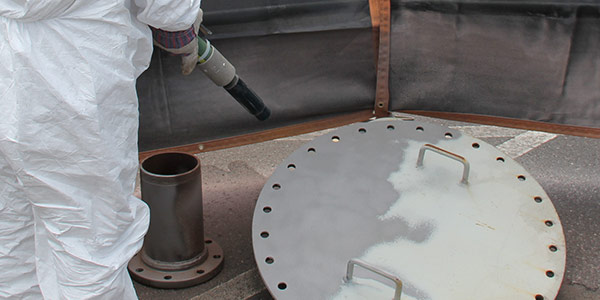
2. Surface Preparation:
Once you have the right plan and the right product, it’s time for the right surface preparation. Inadequate preparation is one of the industry’s leading causes of coating failures. This manifests primarily in two ways; applicator error and/or damage or contamination of the substrate.
Job one of surface preparation is to promote adhesion of the coating to the substrate. Full stop.
If this isn’t done effectively, all following steps in the process are degraded. Coating effectiveness largely depends on whether the coating truly bonds with the substrate or whether it is simply a layer of material on top of it.
Effective surface preparation combines these three elements:
- Elimination of contamination
- A clean substrate
- Creation of a rough profile
Contaminants exist on every surface (mill scale, rust, oxide, dirt, oil, grease, etc.) until they are thoroughly cleaned before application. Contamination can go below the surface as well. For example, salt can be very harmful to protective coatings. If a surface is not properly cleaned and a coating is applied over salt, osmosis can occur which is the transfer of water through a semipermeable membrane from low to high concentration. This causes the coating to bubble in areas with a high salt concentration. Time is of the essence when cleaning a contaminated surface. A blasted or cleaned metal substrate can “flash” rust, meaning rust can form very rapidly and negate the effectiveness of surface preparation.
Creating an appropriate profile for the coating means to “rough up” the surface which allows the coating to achieve what’s called mechanical adhesion. This is when the coating physically locks into the crevices of the surface. A coating can fail if debris, sharp edges, weld splatter or other defects are present on that surface.
The Association for Materials Protection and Performance, or AMPP (a recent merger between the Society for Protective Coatings (SSPC), and the National Association of Corrosion Engineers (NACE)), and the Swedish Standards Institute clearly define surface preparation standards. Your coatings professional should be able to define which standard is optimum for your surface preparation. The higher the standard, the more likely your coating application will achieve the desired results. Consult with your contractor or applicator to determine the best method of surface preparation for your particular job.
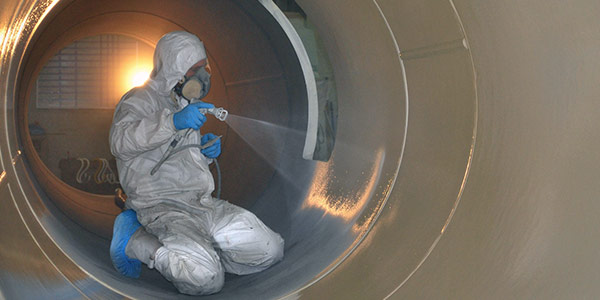
3. Experienced Application:
Experience matters when trying to prevent coating failures in the application stage. Shortfalls in planning and preparation come to light in the application stage when the product cures.
Factors that directly contribute to how a product cures are:
- Ambient temperature
- Substrate temperature
- Working life of the product
- Required product thickness
- Application technique
Your applicator should know the ambient and substrate temperatures from preliminary planning and take those properties into consideration when recommending a solution. If done properly, issues such as fast curing, poor adhesion, and melting of the product can be avoided. Your coatings expert can also recommend methods on how to best control ambient conditions that promote proper application.
Product work life effects the available window in which the coating must be applied and by extension, the haste with which the applicator must work. Coatings with a quick cure time, like emergency coatings, have increased risk of failure due to the shortened application time, if not done properly.
The required product thickness will be specified by the coating’s manufacturer to reach specified metrics for protection against erosion, corrosion, or chemical attack. Failure to meet the specified thickness can lead to reduced life expectancy of the coating, while over application will add to the cost of installation, wasting both time and material.
Application technique is the common denominator in each of these factors; your applicator’s experience level is integral for success and avoiding potential failure down the line.
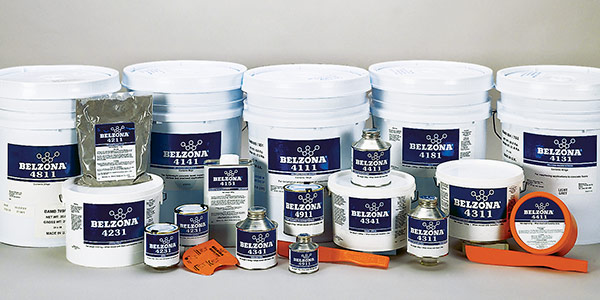
4. Adequate Storage:
In many ways, a coating is like the milk in your refrigerator. It has a “use by” date and needs to be stored within a specified temperature range.
Manufacturers give every product a shelf life that limits how long it can be stored before it loses its effectiveness. Most times, this represents the date by which a manufacturer will no longer warranty their product, so it doesn’t just magically go bad on the expiration date. However, beyond the shelf life a product can interact with moisture, oxygen, carbon dioxide and other contaminants. It can also exhibit signs of skinning, crusting, or thickening. Coatings can also settle or separate, depending on the situation. Generally speaking, a product opened and resealed offers increased likelihood for contamination and ultimately, failure.
Coatings manufacturers typically set the temperature range for storage and deviation from these limits is the far more common cause of storage-related coating failures. Coatings stored at the wrong temperature or moisture ranges can fail because the chemical properties could change, limiting its ability to bond properly. The higher the storage temperature, the more rapidly reaction or change is likely to take place. This can ruin your product even before it’s opened. Lower storage temperatures can lead to crystallization, but this condition usually reverses after heat is added. Unfortunately, you can’t open a coating like a can of milk to see if it passes the smell test when you are close to, or slightly past, the expiration date.
Be sure to review the product’s details with a coatings specialist to ensure that it is appropriate for your project. Ask your distributor if the product was stored properly and if you store products on your shelves after purchase for emergency use, be sure to pay close attention to the limits.
Wear is inevitable, but lining a substrate with a protective coating is an economically friendly method to extend the longevity of a process. To mitigate failure, consult with a coatings expert and contractors who have a consistent track record of quality installations.
The BIG Takeaway
Before you click away to another site, these are your top takeaways from this post:
- When planned, prepared and applied properly, coatings should provide a long lasting solution to your needs.
- Improper assessment of the substrate and lack of surface preparation are the biggest reasons why coatings may fail.
- Consult your local coatings professional with a consistent track record of success before installing epoxies or coatings.
Banks Industrial Group provides protective coating solutions for all your maintenance needs. We can provide the appropriate solution for your protective needs, train your team to apply the solution, or perform it turn-key for you. To learn more about how to properly apply a coating consider scheduling a Lunch & Learn with us! We are happy to teach you the skills you need to prosper!