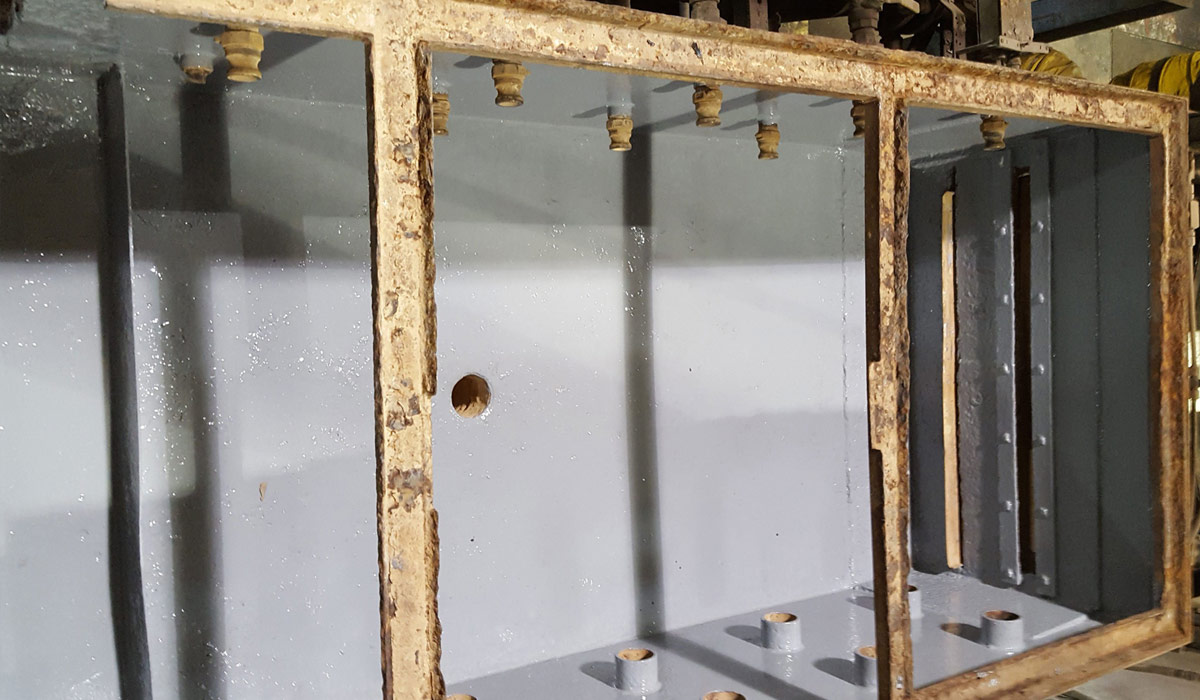
Contents
Repair steel boxes and save them from a near-death experience
Here at BIG, customers ask us to repair steel, concrete and rubber components in all sorts of conditions prior to the repair. Some projects stand out for their challenge and impact. This is one of them.
These pictures show four foot by nine-foot carbon steel boxes used in the manufacturing process for sheet metal. These boxes house a process where a water and bleach rinse solution sprays on sheet metal as it passes through them. As the pictures show, these boxes suffered from years of neglect, corrosion, and deterioration.
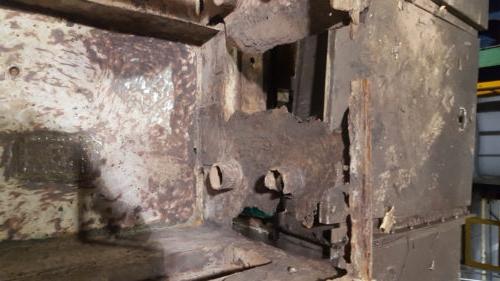
The boxes both exhibited thin-wall and through-wall defects throughout, causing significant leaking for the owner. This leaking caused environmental and safety problems for the customer, as the rinse solution contained diluted bleach. They actually created a make-shift gutter system to contain the leaking solution.
The customer asked BIG to rebuild four sections of the side walls to repair the damaged metal, holes and other sources of leaks. They faced fiscal constraints as well as time constraints for the amount of time they could allow the manufacturing process to go offline. They needed an affordable solution, done quickly, to extend the life of their deteriorated boxes. BIG technicians tackled the problem with a few coatings, stainless steel plate and tools to prepare the surfaces.
Where to start? The steps to repair and reinforce steel containers
1. Grind the boxes to a usable surface and prepare surface of steel reinforcements to make the substrate clean, sound and roughened
2. Clean and de-grease the steel surfaces with a solvent like acetone or denatured alcohol
3. Rebuild the damaged wall areas using cold plate bonding techniques
4. Patch holes and thin-wall defects using carbon fiber/fiberglass wraps
5. Apply an immersion-grade protective coating to line and protect against future decay
Surface preparation allows coatings to bond to the substrate
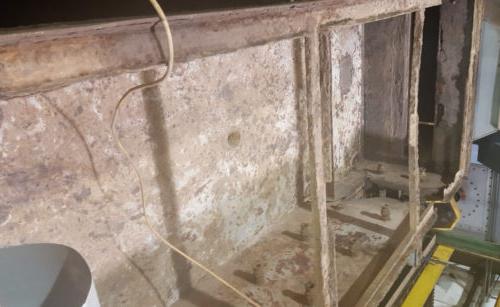
Great surface preparation ranks as one of the most important factors for a repair solution using coatings to stand the test of time. Ideally, surface preparation will leave a clean, roughened, white steel surface. Without a clean, exposed substrate (or the surface underneath all the rust and paint), coatings or epoxies will not perform to the desired levels.
BIG technicians sought to remove years of built up corrosion and paint, hoping to expose a clean substrate. In this case, they used angle grinders to grind down the interior and the outer side walls of the steel boxes. The amount of contamination and damage to these boxes caused difficulties in surface preparation as the remaining steel in each box lacked the strength to resist significant grinding or blasting. Unfortunately, in this case, too much surface preparation would result in making the problem worse for the customer. As a result, substantial residue remained in each box, preventing applied epoxy repair material from achieving an optimum bond (a combination of mechanical, chemical and adhesive bonds) with the steel box.
In addition, the steel plates used to reinforce the side walls required surface preparation with that same grinder. The objective is to rough up the surface significantly enough to allow for the epoxies to achieve a mechanical, chemical and adhesive bond to both the repair plates.
Finally, our technicians needed to remove all of the resulting debris and to thoroughly wipe down the area using a cleaning solvent like MEK (butanone, or methyl ethyl ketone, a common industrial solvent).
Rebuild and repair steel wall areas using cold plate bonding
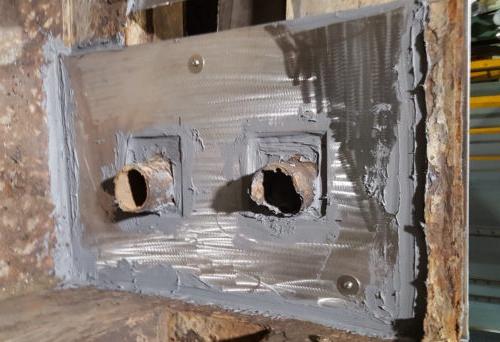
These steel boxes suffered from severe damage on multiple sides, requiring new steel plates to reinforce them. The existing condition of the boxes made welding infeasible. Our technicians used coatings (in this case, Belzona 1121, also known as Super XL-metal) to cold plate bond the plates to the sides of the existing boxes. The Belzona products selected allows for extended working life (up to 35 minutes at a room temperature of 77 degrees F) and for a more surface-tolerant application given the deteriorated and contaminated condition of the steel boxes.
For the areas of the wall completely destroyed or missing, technicians took two steel plates and sandwiched them on either side of the gap, using the Belzona coating in between to hold them together and to bond them to the existing wall. This technique is called cold plate bonding, and it eliminates the need for welding. No welding makes for a safer job and eliminates fire hazards to the surrounding plant equipment. The cold plate bonding method also sped up the repair process, reducing the customer's downtime.
For one particular set of plates, we bolted them together to add mechanical strength and help set the plates in place prior to bonding them using the Belzona epoxy.
Patch holes and reinforce the existing steel boxes using carbon fiber/fiberglass wrap
Smaller holes required patches to contain moisture and the overall structure needed support to maintain some degree of integrity. Our technicians used a carbon fiber wrap (in this case, the Belzona Super Wrap II system, consisting of a resin system and composite cloth) to patch smaller holes and reinforce the damaged walls and floors.
Apply an immersion grade protective epoxy coating to prevent further damage
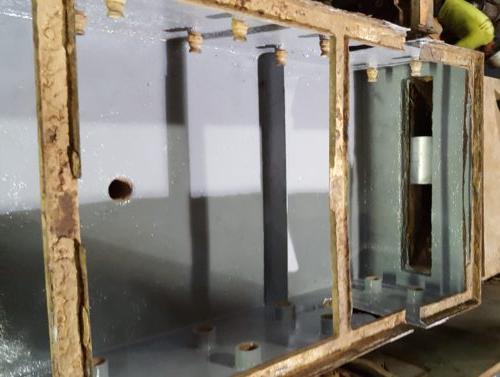
Finally, our technicians coated the entire interior of the boxes in order to prevent further damage to the boxes. They chose Belzona 5811 to provide chemical resistance to the bleach and protect the steel while submerged in aqueous solutions from corrosion. In addition, they chose this product for its easy application and quick curing process, reducing the customer's shutdown time.
How did this solution impact the customer?
The customer needed this job completed within a short time frame during their planned shutdown period. They could not afford for this equipment to go offline for longer than a few days. Both fiscal and time constraints made outright replacement a difficult proposition. The environmental and safety impacts created additional urgency. Adding to the matter, the condition of the boxes prevented optimal surface preparation needed for optimal performance by epoxy coatings. So, in this case, the pre-existing condition of the boxes, the time constraints of the shutdown period, and the environmental/safety considerations contributed to a less-than-perfect repair solution.
BIG completed this job for just under $9000 and in only two days. We met both of the customer’s critical constraints and allowed their operations to resume on time and within their budget. The customer’s operations manager estimated replacement of these boxes at multiple times the amount needed to repair them.
In addition, this solution corrected the environmental and safety problems created by the leaky steel boxes.
Want to know more?
Do you have similar problems? We would love to hear about them and help you find solutions. Schedule a lunch and learn with our team today. We will provide lunch and information on solutions to help you meet your repair and maintenance needs.
Email or call us at 856-687-2227 now for assistance!