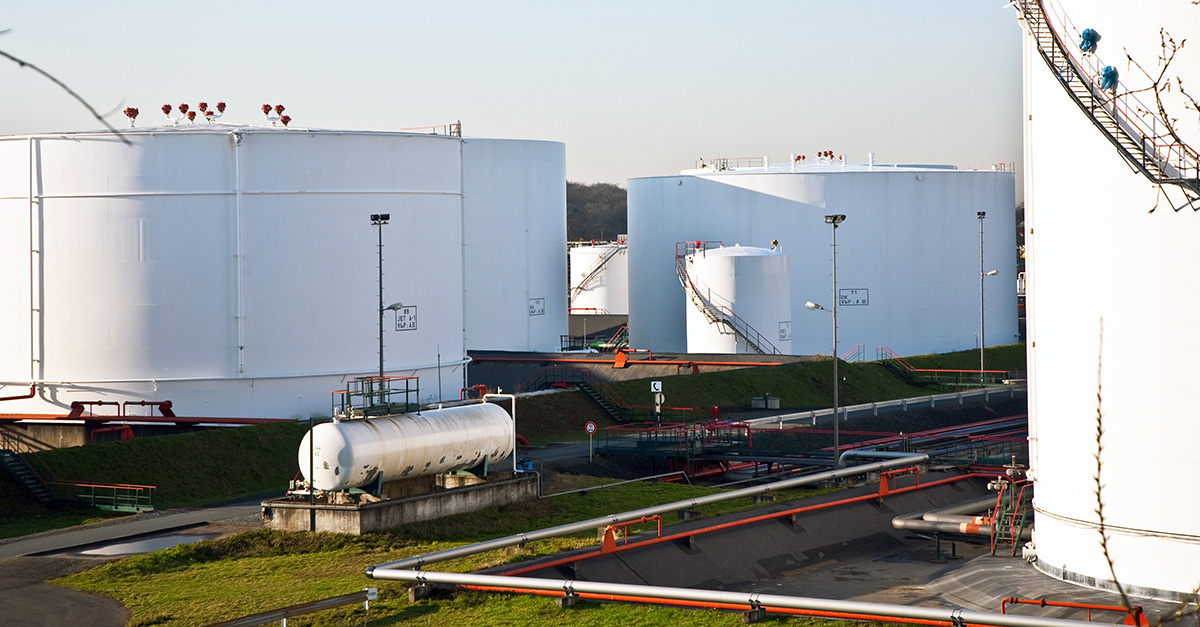
Contents
When, why, and how an SSC should be a part of your operational safety protocol
When it comes to regulations, designs, and requirements, the secondary spill containment (SSC) landscape is a bit like the wild, wild West. Governing bodies such as the Environmental Protection Agency (EPA) and Occupational Safety and Health Administration (OSHA) don’t have specific guidelines on how secondary spill containment should be implemented, only if and when there must be one and what parameters it must meet to prevent the worst case scenario from happening. Without those “two Sheriffs in town,” so to speak, individual facilities are responsible for designing SSC to meet the unique needs and physical attributes of their own location. The EPA and OSHA do dictate the baseline spill volume a certain facility would need based on their output, along with how that spill volume should be properly handled and cleaned up. The EPA focuses on oils and spills into waterways, while OSHA addresses the release of harsh chemicals. Still, the actual design, construction, installation, and operation of the secondary containment system falls to each company. The professional engineer (PE) on your project will typically consult with you on the proper size of your containments to mitigate your risk. Once designed, Banks Industrial Group can assist your company in navigating that space to ensure your SSC meets or exceeds all EPA and OSHA requirements.
If you’ve landed on our informative article via a search engine and you’re still relatively new to what a SSC is, let’s clear that up before we go any further. In theory, SSC is quite simple; it’s a containment featuring any configuration of metal, concrete, plastic, resin, or other durable material that is designed to stop a spill from leaving its primary area and causing harm to the people or surrounding environment. Sometimes the primary container, such as a tank, tub, or silo, is stationary and on the ground, immovable. Sometimes the primary container is on a train or other transportation mode, so that consideration must be taken into account when secondary containment is designed. It essentially provides redundancy to the primary container that holds whatever substance, chemical, oil, etc., is used in your operational processes. It may be as low-impact as a plastic tub underneath an oil drum or it may require a highly-engineered solution that can address liquids, solids and gases all at once.
Here is a quick overview of common SSC systems:
- Diking & ditching
- Dedicated sewer systems
- Curbing or drip pans
- Sumps & collection systems
- Weirs, booms, other barriers
- Absorbent material
- Materials that solidify the spilled substance (i.e.: sand, charcoal, etc.)
- Materials that suppress vapor generation
- Neutralizing agents
What are primary considerations in a secondary containment system?
In general there are three; size, material, and shelf life. The companies that invest well in all three areas upfront greatly lower their risk of system failure, environmental damage, lost productivity, punitive fines, and costly cleanup.
Getting the SSC size right needs to be job one.
Size:
Getting the SSC size right needs to be job one. Case in point; in 1988, Ashland Petroleum in Floreffe, Pennsylvania, suffered a catastrophic system failure when one of its massive diesel storage tanks collapsed, releasing 3.8 million gallons of diesel fuel. Their secondary spill containment filled at 2.5 million gallons, leaving over one million gallons to flow over and into the nearby Monongahela River. The environmentally devastating 6-inch oil slick eventually made its way to the Ohio River, impacting the water supply of at least 23,000 surrounding residents and the habitats of countless local wildlife and aquatic ecosystems. In the end, the tab for fines and cleanup topped 18 million dollars.
It’s worth noting here that the EPA gives guidance on what is called “sufficient freeboard” to accommodate storm waters. The guidance may vary slightly; sometimes referred to as 110% of capacity or, in other resources, it says to plan to the standard of a 25-year storm. As you can see, designing and accurately sizing your SSC is critical. Your PE will take the following into consideration when consulting on your containment design:
- Anticipated quantity size needed
- Typical failure modes of that size and containment material used
- Anticipated flow rate of a leak
- The average response times in a customer’s area
- Projected duration of a leak until it is stopped.
Responsible contractors can complement your PE’s design consultation by recommending and installing the right materials to ensure your company’s local and federal compliance, as well as, repairing existing, damaged, or worn SSC systems. Be sure to choose a contractor experienced in installing materials to best defend against common industrial hazards such as sulfuric acid, sodium hydroxide, ammonia, salt, alcohols, hydrochloric acid, sodium hypochlorite, and fuel oils.
Materials:
While the Ashland Petroleum case is a stark example of how size truly matters when it comes to SSC, its design must also be built and maintained to ensure continued structural integrity.
Examples:
- Concrete: If a concrete containment area has slabs joined by caulk, you must routinely inspect that caulk line to ensure it’s not cracked, flaking or worn.
- Metal: If a system is metal with welded joints, those joints must be monitored for stress fractures and cracks.
- Chemicals: Chemical containment areas must be checked for acid and chemical scarring, microbial degradation, corrosion, and abrasive wear.
If a SSC is outside, then elements like the sun, rain, snow, and seasonal temperatures factor into consideration. Think about a railcar filled with a corrosive chemical by way of a retractable arm that swings out and over the rail car. It’s expected that droplets may fall to the secondary spill containment surface beneath that arm. Since this surface sits outside under the sun, next to hot metal tracks, and endures year-round weather conditions, it should be inspected consistently for potential failure signs. Tiny cracks and other degradation can allow the corrosive chemical to escape the SSC and enter the environment (along with potential water tables) beneath the tracks. (This is a great place to mention our blogs on why concrete and coatings fail and the signs to watch for, check them out!)
In cases where concrete or metal provides the primary SSC capability, such as a truck loading zone or the floor of a food processing plant, coating the surface is one way to mitigate small cracks and other potential failure risks. Applying special coatings can make the surface impervious to highly caustic chemicals, such as sulfuric acid, and durable for many years whether it’s exposed to outdoor elements, indoor wash downs, or minor spills and droplets. The coating also keeps spills from soaking through the SSC, instead “floating” on the surface of the coating, making cleanup much faster and easier.
The importance of having a coating is clear, but having the right coating is paramount.
The importance of having a coating is clear, but having the right coating is paramount. Careful consultation with a coatings expert (preferably someone certified by NACE/SSPC or AMPP) is strongly recommended, focusing on these key factors in selection:
- Operating temperature of the material to be contained
- The pH or acidity of the material to be contained
- The type of contact and coverage required (full immersion versus something less)
Ask your coatings professional what type of testing the material selected has endured when choosing resistance to acids; the duration, the level of immersion, and the concentration. While not every scenario can be tested to mitigate your risk, it is important to discern between coatings which have been subjected to rigorous testing for long periods of time in poor conditions against those that are not (or simply not tested at all).
See our post Why Protective Coatings Fail to get insight on the proper planning, preparation and application of a protective coating.
Honest assessment of the concrete, or substrate, before coating application is crucial.
Concrete damaged by acid spills is patched then covered with a protective coating.
Additionally, conducting an honest assessment of the concrete, or substrate, before application of the coating is also crucial. Coatings, while highly effective, do not perform miracles. Pre-existing conditions of the concrete need to be revealed and discussed openly; was it ever exposed to salts, acids, other chemicals, etc.? You may find you need to remove the substrate and pour new material in order to safely accommodate the coating and provide containment. The EPA offers a helpful checklist (Section 4.3.1) for what an inspector looks for when evaluating a containment project. Here are a few highlights:
- Cracks in containment system materials (concrete, liners, coatings, earthen materials)
- Discoloration
- Presence of spilled or leaked material (standing liquid)
- Corrosion or erosion of the system
- Presence of debris
- Location/status of pipes, inlets, and drainage around and beneath containers
- Excessive vegetation that may inhibit visual inspection and assessment of berm integrity
- Drainage records for rainwater discharges from containment areas
See our post The Top 3 Reasons Concrete Fails to gain an understanding of the mechanisms that damage concrete.
Lifespan:
We’ll be frank here, predicting the lifespan of any SSC can be a gamble, especially if the history of the substrate, coating materials, and maintenance track record are not fully known. Designing, building and reinforcing your SSC with all of the considerations discussed, thus far, is crucial. Routine inspections to catch any degradation, cracks, or structural anomalies early are equally paramount. Everything from routine caulk replenishments to assessing operational changes that may require bigger repairs and re-coats make the difference in a 20-year solution lasting its full potential, or degrading in just 3 to 5 years. As we’ve touched on already, but certainly bears repeating; honest assessment of conditions in the design phase, selection of the proper materials for application, and proper maintenance annually, with updates as required, will help give you maximum life and value out of your SSC.
Does my facility need secondary containment?
There may be many scenarios in which secondary spill containment is a sound option for your daily operations, however if you have the following, it’s most certainly prudent and responsible to install one;
- Bulk storage tanks
- Mobile/portable storage containers
- Refuelers
- Tank trucks
- Loading and unloading areas
It’s always worth the consultation, because the flipside of not installing a SSC can be catastrophic structural or environmental damage, massive fines and penalties, multi-million dollar cleanup costs, major downtime for rebuilding, and increased maintenance.
The BIG Takeaway:
If you take nothing else from this blog, keep in mind the following:
- Size of the containment is paramount and should be professionally recommended by the right engineer
- Coatings can extend the life and performance of your containment, but ensure you select the right types with proven test results for the operating conditions of the environment
- Coatings will only perform as well as the underlying substrate. Make an honest assessment of the substrate from a trained professional before choosing a coating material
Let Banks Industrial Group find the most cost-effective and operationally sound SSC solution for you. We invite you to view our webinar on Secondary Spill Containment systems and our detailed solutions for a variety of industrial settings. For more information please contact us.