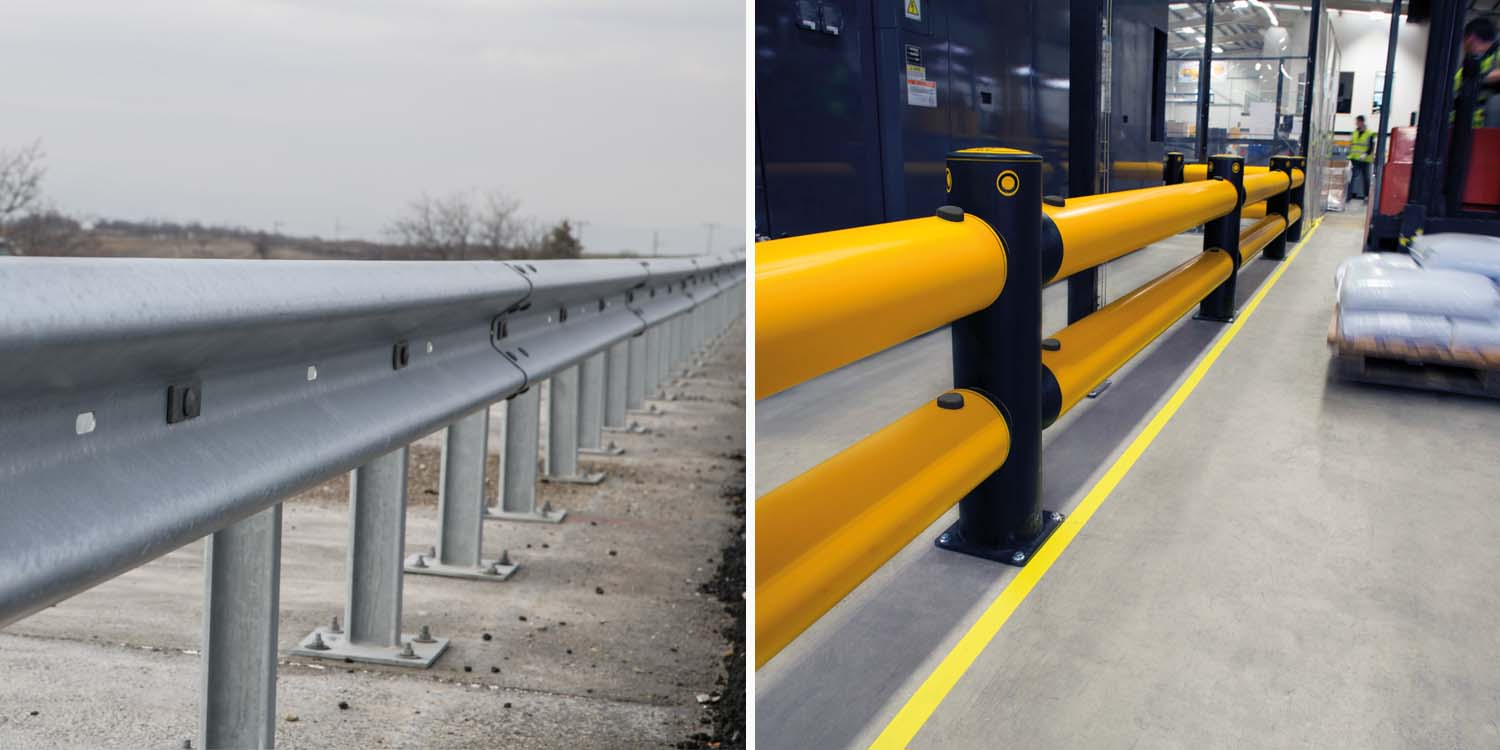
Contents
Hard hats, painted floor lines, warning signs, lock out-tag out procedures, handover briefings…these are all hallmarks of a good workplace safety program.
However, in most industrial settings, good is not good enough to fully protect today’s workers.
In most cases, physical barriers are also needed to properly direct vehicle and pedestrian traffic, visually signal danger points in an environment, and better protect machinery and infrastructure during collisions, to name just a few applications.
The Occupational Safety and Health Administration (OSHA) notes that traditional approaches to safety are often “reactive”; meaning, a worker gets sick or hurt or assets are damaged and productivity is lost before assessments and improvements are made. Installing adequate physical safety barriers is a crucial step in mitigating that risk. OSHA guidelines state that guardrails must be made of materials that not only stop the force of a fall or collision, but also do not cause harm to employees. OSHA article (1926.502(b)(6)) lists these as punctures, lacerations, falls, clothing snags, and shock force from a collision. Depending on the materials used in the barriers and those of the surrounding collision site, energy can be transferred to the human operator and load being carried. These collisions could result in lethal injury to the driver and costly damage to the goods that topple from the lift. Facility owners need to consider the best material for safety barriers to prevent those outcomes.
Each year, OSHA updates their most common causes of industrial site deaths. Among this list is OSHA’s “Fatal Four”, the top four leading causes of worker deaths in construction that translate to just about every industrial, manufacturing, and warehouse distribution setting.
- Falls (33.5%*)
- Struck by an object (11.1%*)
- Electrocutions (8.5%*)
- Caught in/between (5.5%*)
*Percentage of accountable deaths on average annually
In 2019, OSHA reported that 5,333 workers died on the job which translates into more than 100 a week or 15 fatalities a day.
In two of those “Fatal Four”…struck by an object and caught in/betweens…enhanced and appropriate physical barriers could reduce those fatalities year over year.
What do we mean by “appropriate physical barriers”?
Guard rails, bollards, and pallet rack leg guards increase protective measures for humans, machinery, and structures in a workplace. Painted lines on a floor are a good start, but they encourage people to look down, not around them. When workers are in moving vehicles, primarily forklifts, they need above-ground, highly visible indicators on how and where to operate safely – like the barriers we put on roads, bridges or even in parking lots. Steel and polymer are the two most common materials used today in worksite safety barriers.
STEEL: It’s as American as apple pie and the 4th of July. Different styles of fabricated steel guard rails were first developed in the early to mid-1900s for use along the nation’s highways and agriculture. These rails, strong and cost-effective, were soon adapted for safety purposes in industrial settings. They are still the dominant choice for workplace safety barriers today.
POLYMER: In the latter half of the 20th century, plastic and polymer versions of safety barriers started to gain popularity as an alternative to steel for a variety of reasons.
Let’s explore the pros and cons of each:
Steel Guard Rails
What’s good?
- AN INDUSTRY STANDARD: Steel is still the prevalent choice on most construction, industrial, and manufacturing sites today.
- INITIAL COST: It’s considered to be a strong and acceptable choice, while also being relatively low-cost up front and disposable when damaged or worn.
What to consider?
- DURING IMPACTS: Steel simply isn’t designed to protect against the much higher forces and more powerful vehicles used in modern industrial environments. When there’s a collision, you’re left with a damaged or destroyed barrier, along with any vehicle, infrastructure impact, or production downtime associated with it (or the added expense if damaged machinery belongs to an outside vendor working on your site).
- DURABILITY: Steel is subject to denting, rusting, and chipping, requiring preventative maintenance more often and that runs up the tab on yearly operational costs. Over time, that rusting, denting, and chipping can make the barriers less visible which poses a higher risk to operators and pedestrians.
- FACILITY DAMAGE: Steel is very rigid and unyielding, transferring any impact energy into the surrounding floor and other structure. These repeated impacts over time can prematurely damage your concrete, causing more expensive maintenance and repairs sooner.
- VISIBILITY: OSHA regulations (article 1910.144(a)(3)) dictate that safety barriers be yellow, “the basic color for designating caution and for marking physical hazards…” Since painted steel chips and fades over time, routine repainting and maintenance costs are higher and require more of the annual operating budget.
Polymer Guard Rails
What’s good?
- DURING IMPACTS: Polymer doesn’t just stop the force of an impact, it absorbs and moves with it. This means during a collision, the barrier takes the force of the blow, flexes, and returns to its original shape with little to no damage on the machine that hit it or the environment around it. Polymer blends, like A-SAFE’s advanced Memaplex, which is three times stronger than steel, cushions these impacts (up to 80%) and mitigates physical damage to the machines and vehicles during contact.
- ELIMINATE IMPACT SHOCK: Collision energy isn’t transferred to the floor, surrounding structure, machinery, or vehicles. It’s confined within the barrier itself, protecting the floor from premature damage and removing the risk of impact shock to operators and loads. Read here about how concrete fails in general to learn how damaged concrete drives up your operational costs in a number of ways!
- DURABILITY: The bright polymer coatings make them highly visible and easy to see by workers from all angles. Unlike painted steel, this color stays intact and vibrant for years, improving guidance to workers and pedestrians through and around the worksite and keeping OSHA compliance regarding barrier visibility on point. Additionally, companies using polymer save on operational costs annually by eliminating the need to repaint, repair, or replace steel barriers.
- TESTING: A-SAFE conducts standardized, realistic testing to PAS 13 compliance, which is published by the British Standards Institution (BSI) and considered the world’s first and foremost safety barrier testing code in industrial workplaces. All impact products are subjected to rigorous, repetitive collision tests and measured against a high standard of performance and recovery. The tests are monitored by TÜV Nord to receive their independent verification that A-SAFE products reach the industry’s highest standards. You can read more about A-SAFE’s product testing practices and standards here.
- FOOD AND MEDICAL ENVIRONMENT SAFE: Polymers perform better in the highly regulated and demanding environments of food processing and healthcare. Both have hygiene requirements that demand much higher performance standards. A-SAFE’s specially designed hygiene seals prevent the ingress of moisture, bacteria and dirt, while the polymer material is chemical resistant, scratch-resistant and non-corroding. The products are self-colored and do not need painting, eliminating the risk of cross-contamination from rust or paint particles.
What to consider?
- INITIAL COST: Initial investment and installation of polymer guard rails, bollards, and rack protection is typically more expensive than steel out of the gate. A facility manager would need to run the numbers on total cost of ownership to see how soon polymer options could “pay for themselves” when compared with the annual maintenance, repair, liability, and replacement of steel counterparts.
Whether a company chooses steel or polymer, there is one unifying safety investment every industrial worksite can make; training equipment operators to drive carefully and obey all worksite traffic regulations. Safety barriers need to be effective, but the aim must be to avoid hitting them in the first place.
The BIG Takeaway
This was a lot of information (we get it!), here are your Top 2 Takeaways:
- Something Over Nothing: Both steel and polymer safety barriers will help your company meet local and federal “appropriate physical barrier” requirements. Assess your operational areas where foot and vehicle traffic intersect and ensure there is proper protection there. Bottom line, either type is better than NO type when it comes to making your work environment safer.
- Total Cost Ownership: Take time to consider more than immediate procurement costs. Look long-term at the maintenance needs and durability of the barriers you select to make sure the impact on your operational budget stays within range well beyond the first couple years after installation.
Interested in learning more about steel vs. polymer barriers? Banks Industrial Group provides single-source service for sales and installation of A-SAFE guard rails and safety barrier systems. We are safety-oriented, ISNetworld certified A+, and fully insured to reduce your risk. Please contact us today for more information or to schedule service.