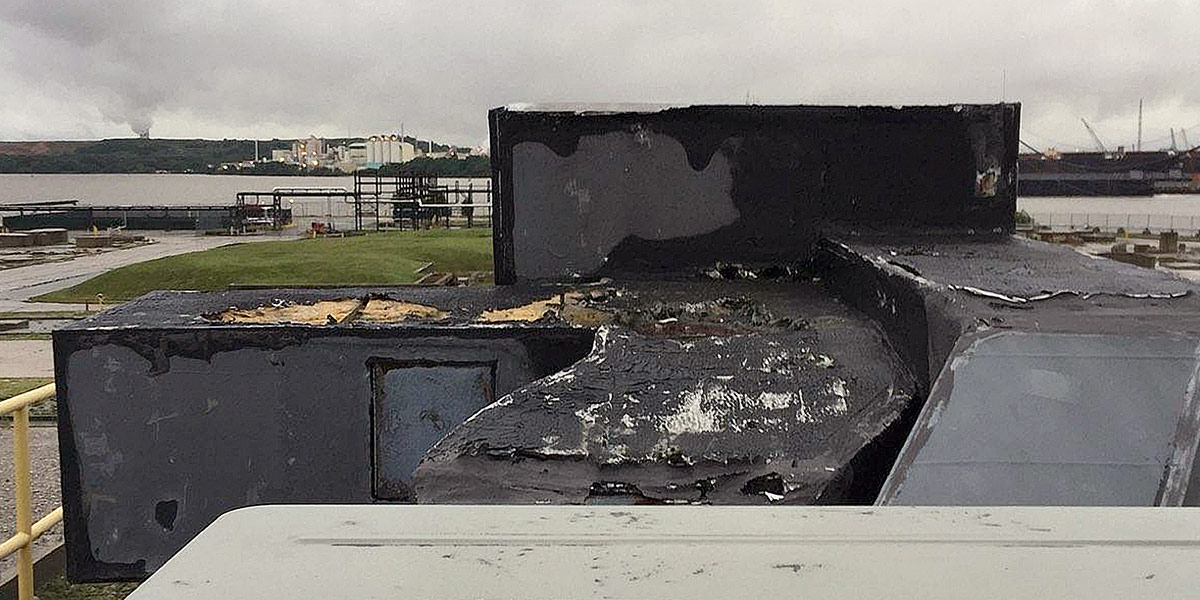
Contents
It’s probably one of the most important systems in a commercial or industrial facility that is rarely seen and thought about even less; the ductwork. While it may be out of sight, out of mind, it’s critically important to daily operations on many levels; safety, climate comfort, energy efficiency, cost control, air quality and more. In many cases, ductwork doesn’t land on a facility manager’s radar until energy bills increase, HVAC performance drops, or indoor air quality declines. Ductwork is usually behind walls, suspended from the ceiling, or stretched over rooftops and designed from a myriad of different materials. If ductwork is properly insulated and sealed, it can prevent leaks and optimize efficient airflow. When ductwork is not properly made or installed, it becomes an expensive and invasive issue to correct.
Before we look at the typical ways in which ductwork can fail, let’s review the most common materials used in duct networks.
Galvanized sheet metal (most common material used) or aluminum (used in 1%-2% of applications) make rectangular sheet metal ductwork. While aluminum can be lightweight and easy to install, some sheet metal ducts can be heavy and take up more space than other materials. Both require support to tie them into the building as required by the Sheet Metal Air Conditioning Contractors National Association (SMACNA).
Flex ducts (rarely used in commercial applications, and usually only in short lengths) come in tube-shaped systems made of wire enclosed in plastic and covered in insulation. Some construction designs make it challenging to install rigid ductwork, so contractors will then use flex ducts. During installation, contractors try to prevent kinks, excessive bends or dips in the flex duct that obstruct airflow. They will also try to limit the length used to prevent friction and promote smooth airflow through them.
Fiberglass duct boards are designed using grooved cuts and then folded in a way that promotes an air tight seal and better delivery of conditioned, cooler air to the targeted space without leaks. Since the boards are made of fiberglass, good insulation material, the product maintains its temperature better than standard, uninsulated metal ducts. These attributes make these duct boards a good candidate for use with smaller-sized heating and cooling systems.
Phenolic ductwork (AKA Kool Duct) is known to have some of the highest R-values available with an aluminum liner that allows air to pass over a clean, smooth surface. This removes the need for fibrous, open cell insulations, raises the indoor air quality (IAQ) of the spaces it serves, and prohibits the growth of mold and bacteria. Along with offering R6, R8.1, or R12 insulated values, it’s also UL 181 listed. Since it is pre-insulated, it doesn’t require additional space for separate insulation, meaning it can be stacked or installed flush to the ceiling which saves valuable building space. It’s fire retardant, light-weight, and achieves a SMACNA Class 3 leakage rating.
The “R” in R-value stands for resistance; usually expressed by a numbered rating. The Industrial Energy Conservation Code (IECC) establishes regulations for R-value based on climate zones. The IECC sets the standard at R-6 for indoor zones and R-8 for outdoor zones in warmer climates. They set the standard for colder climate zones at R-12. The numbers assigned relate linearly; for example, R-16 insulation offers twice the resistance of R-8 insulation. Traditionally, insulation for ductwork includes loose-fill material such as fiberglass or elastomeric foams. A reminder, if your duct is phenolic, then the duct is inherently insulated. Typically, the thicker the insulation, the higher the R-value.
Here are some factors which lower or deteriorate insulation’s R-value:
- Material compression: Some insulation relies on tiny pockets of air to slow the gain of radiant heat. Compressing the material condenses those pockets of air, reducing their effectiveness. Compression is often caused by people stepping on top of wrapped ducts or pipes or the weight of standing water or snow atop exterior ducts.
- Raised surfaces on the ductwork: Insulation must be routed in a way to accommodate raised surfaces such as a transverse duct joint (TDC). When insulation is routed to pass over the joints, the R-value is lowered due to reduced thickness, allowing for localized condensation to form around the joint.
- Exposure to moisture: Nothing kills the value of insulation more than moisture. Moisture erodes up to 80% of the insulation’s effectiveness. To make matters worse, wet insulation blankets metal ducting and increases the likelihood of corrosion, mold, and mildew.
What are the considerations with outdoor ductwork?
When dealing with exterior duct work, there are specific insulation guidelines to follow. We recommend checking out the code notes on commercial duct installation and sealing as laid out by the U.S. Department of Energy.
Some highlights:
- Supply and return air ducts and plenums need to be insulated with a minimum of R6 insulation if located in unconditioned spaces or when located outside a building with a minimum of R8 insulation in climate zones 1-4 and a minimum of R12 insulation in climate zones 5-8.
- If located within a building envelope assembly, the duct or plenum needs to be separated from the building exterior or unconditioned space or exempt spaces by a minimum of R8 insulation in climate zones 1-4 and a minimum of R12 insulation in climate zones 5-8.
As with most things, there are exceptions to the rules; duct work located within equipment or in places where the temperature difference between the interior and exterior of the duct or plenum is less than 15°F need more help identifying what counts as “unconditioned” or “exterior”? There’s a regulation for that, too! ASHRAE 90.1 2016 code defines exterior spaces as including “attics above insulated ceilings, parking garages, and crawl spaces, as well as spaces outside the building envelope, such as rooftop ducts.”
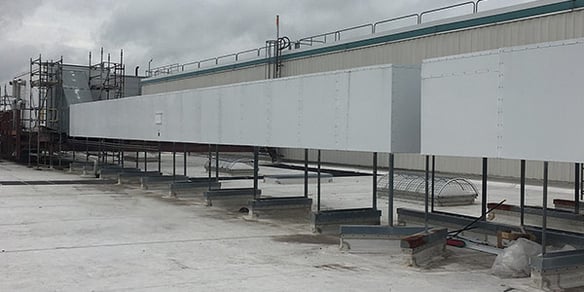
How can a business better the odds their ductwork will stand the test of time?
Two key ways; proper insulation and regular testing.
Insulating the Ductwork
There are no downsides to good insulation when it comes to ductwork. Proper insulation lowers energy costs, minimizes condensation buildup, provides a barrier to temperature differences, minimizes corrosion and mitigates the dispersion of mold and mildew. Additionally, periodic cleanings of the ductwork can remove bacteria and dirt that build up in the ducts and prohibit adequate airflow.
Ductwork should be insulated in any environment where the potential for temperature differences between indoors and outside exceeds 15°F. Proper insulation will reduce the strain on your HVAC system as it keeps it from overworking to maintain the desired heating and cooling levels.
See our post How Wrapped Insulation on Rooftop Ducts Fail for a better understanding of the mechanisms that can damage insulation.
Balancing the System
While it’s difficult to “test” the system after insulation because the leaks won’t be detectable, you can balance the system by checking airflow which could help pinpoint any lingering issues.
If you find the airflow balance is off it could mean your air handlers are not putting out the proper cubic feet per minute, or CFM. Testing, adjusting, and balancing an HVAC system is critically important because it will ensure the entire system delivers the optimum airflow in line with the manufacturer’s design specifications.
Balancing the system should cover:
- Fan speeds
- Power usage
- Control settings
- All air supplies; return, exhaust, outdoor
- Air temperatures
- Filters or collector resistance
The three main objectives of balancing a system is verifying the system delivers the most operational efficiency for its design, find and fix any existing problems, and ensure the system is safe.
If a leak is found an air conditioning professional can seal it with mastic (a caulk-like substance) or a specially formulated duct sealant. In some cases, mastic tape or foil tape can be used.
If ductwork is properly installed, insulated, and tested, why does it fail?
The primary suspect in most ductwork failures is something wholly preventable. Lack of maintenance is a major cause behind small problems evolving into big headaches for facility managers. Properly installed, sealed, and insulated ductwork should last for 20 to 25 years.
It’s important to take note that when upgrading your HVAC to a newer, high efficiency system, older ductwork may need to be replaced because it’s too narrow to handle the increased airflow.
Here are other reasons ductwork fails:
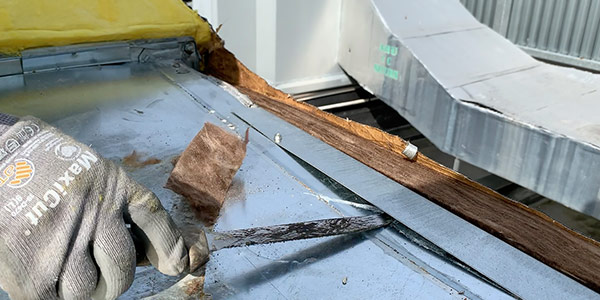
Improper Sealing
Duct joints are the weakest link in the system. Improperly sealed joints can lead to moisture intrusion, lower quality of air, and higher energy bills. Since sealing is done at the point of installation, it’s paramount that this be performed meticulously and precisely.
Today’s market only accepts leakage rates of 1% to 3%, which is challenging with sheet metal ducts. Hospitals ideally want no more than 1%. The old market standard was 5% to 10%, so you can see how much more narrow the margin has become and with joints never being perfectly square, precision sealing is mission critical.
Duct joints should be secured with screws and sealed (to SMACNA standards) with a UL 181 rated tape or mastic. Larger gaps should first be reinforced with fiberglass mesh tape before applying the mastic. Weather extremes also impact joints, especially exterior ducts. In winter, sheet metal expands when warm air passes through and contracts when it cools. In summer, sheet metal contracts when cool air passes through and expands when it stops. This constant expansion and contraction causes wear and tear on joints.
Joints can leak in the supply and return side plenum, as well as the duct trunk. The supply plenum distributes warm or cool air, and the return plenum sends the air back into the HVAC system to be recycled. The duct pipes connecting to the main trunk can also leak air frequently at the joints.
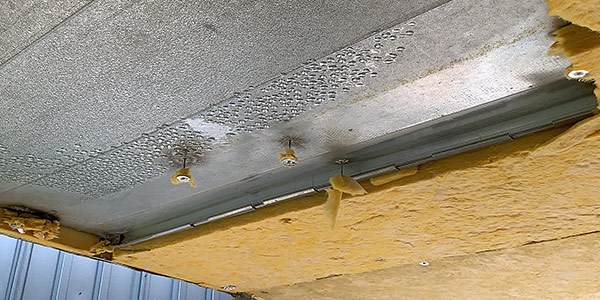
Condensation
A quick note on both internal and external condensation.
Internal condensation occurs less frequently because the airflow in the duct dries the moisture out before it can completely form.
Internal ducts that are known as “open air” won’t typically have insulation on them as the space they are in is climate controlled and won’t cause the 15 degrees, or more, difference between the duct and surrounding air.
One note here, however, is if the duct is near a hot roof in the summer time, the duct can experience sweating because it is not insulated.
External condensation occurs from improper insulation, improper installation, R-value, etc. You will see the results of exterior condensation with stains on ceiling tiles (when ducts are behind drop ceilings), on drywall, on the floor, and other areas. This can be a common mistake in building renovations when new ceilings are put in, but the existing ductwork, now enclosed above the ceiling, is not insulated because it was previously considered “open air” and would have been within the 15-degree temperature variance of the surrounding space.
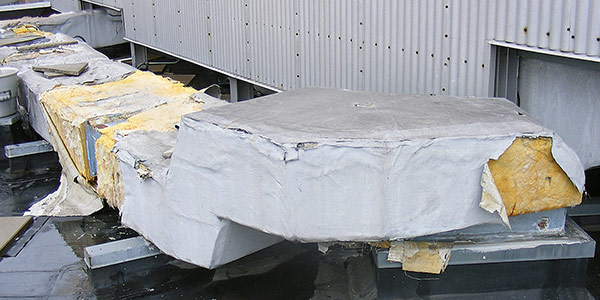
Lack of Maintenance
When properly installed, sealed and insulated, ductwork should last for 20 to 25 years. Properly maintaining the ductwork by checking for air leaks, moisture, and corrosion can help prevent premature failure of the entire ductwork system.
Replacing the HVAC system itself with a new high efficiency unit may require replacement of ductwork. For example, aging ductwork might be too narrow to handle the higher airflow of a new, efficient HVAC system.
It also may be beneficial to periodically clean the duct system. Bacteria and dirt can build up in the ducts and block air from pumping out of vents properly.
See our post Indoor Air Quality and Workplace Health to gain a better understanding of how deteriorated ductwork impacts IAQ.
The BIG Takeaway
Here are your top takeaways for all of the information presented above:
- Moisture kills insulation, eroding up to 80% of the insulation’s effectiveness.
- There are no downsides to good insulation when it comes to ductwork.
- Precision sealing of ducts drives efficiency.
- When properly installed, sealed and insulated, ductwork should last for 20 to 25 years.
BIG SOLUTIONS
If the ducting in your facility or the insulation displays any of these tell-tale signs of failure, Banks Industrial Group can provide you with affordable and customized solutions to re-insulate or replace your ductwork. We’ll help you double the industry standard for R-value, reduce air leakage to less than 1%, and keep your ducts moisture-free through a triple-sealed system that’s warrantied for 20 years. For more information please contact us or visit our HVAC Duct Insulation webpage.
Sources:
https://www.hvac-for-beginners.com/duct-board.html
https://www.hvacductsystem.com/koolduct/kingspan-koolduct-features-benefits-of-phenolic-ductwork
https://www.cfmtest.com/testing-and-balancing