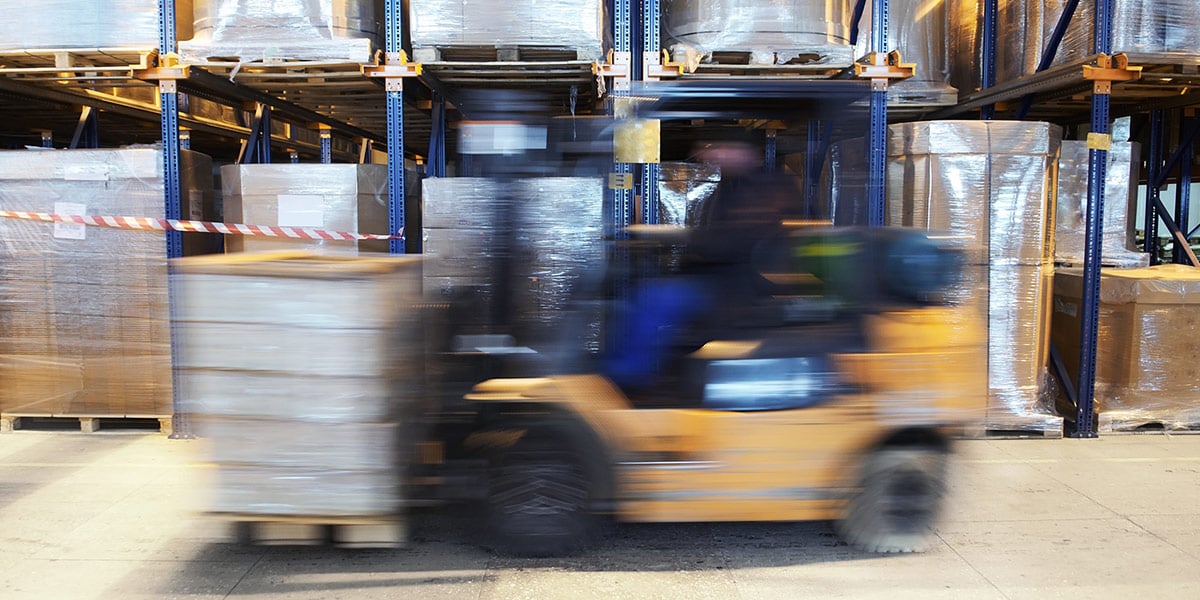
Contents
How concrete damage and poor expansion joints drive up the cost of warehouse operations
Ignoring routine preventative maintenance runs up the tab on operating costs well beyond the repairs needed to a facility’s physical infrastructure.
Case in point; while touring a customer’s warehouse facility recently, I watched multiple forklift drivers racing product back and forth on a proverbial “highway” created between various rooms in the facility.
Two things stood out to me immediately:
- The forklift operators drove really fast, regardless of the amount of the product on their forks.
- The operators frequently swerved their trucks at the same spot during every trip.
The speed of the forklifts reflected the pace and pressure of operations, the skill of the operators, and perhaps the safety culture at the facility. The speed was somewhat understandable. The swerving, however, was not. I went to investigate.
When I stood at the spot on the “highway” where the operators swerved, the cause was glaring; poor expansion joints.
Each expansion joint in the floor was becoming a relative “canyon.” What started roughly as a half-inch gap between concrete slabs had now widened to several inches, all uneven and jagged. I asked the facility manager how the joints arrived at that condition and he told me that the pallet jacks - with smaller wheels – cannot bridge the width of the joint and, on each passing, this causes chips along the edges of the concrete slabs. Over time, the expansion joint gap had widened to the point that not even the larger forklift tires could drive over them without experiencing the impact of excessive concrete spalling.
If the cracks don’t slow operations, are they a priority right now?
Yes. Here’s why;
Fast-moving forklift drivers who swerve to avoid large gaps take a safety gamble with every single pass. Sudden movements at high speed can cause a loaded forklift to topple or flip if the center of gravity shifts. In high traffic environments, drivers passing left to left can’t always swerve, as they may collide with infrastructure or with each other.
In the most likely scenario, the forklift hits the “pothole” of spalled concrete or busted expansion joint over and over again. This can quickly erode or even blow out the tires of the forklift. While the cars we drive to work can better handle high speeds over potholes for up to 60,000 miles, smaller forklift tires simply can’t take that kind of abuse without the benefit of larger tires with suspension or shock absorbers.
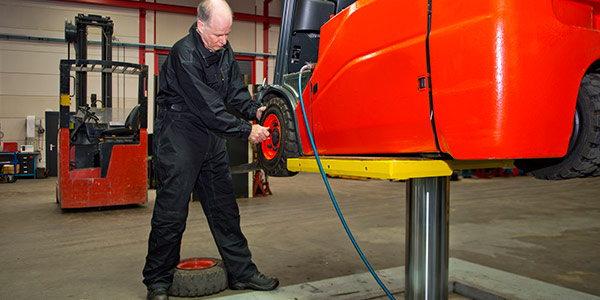
How does this translate to higher overall operational costs?
The higher costs in the most dangerous scenario are hard to quantify, as most safety risks are, however an owner in this scenario can be liable for the following:
- Operator injury or fatality
- Repair to a damaged forklift
- Repair to damaged equipment or infrastructure from a collision
- Loss of product
Safety reporting in the U.S. shows these risks to be a common and expensive problem. According to 2019 USG data on reportable incidents, forklifts were involved in 8,140 non-fatal injuries (note: OSHA estimates that non-fatal injuries go unreported by up to 50%) and 79 work-related fatalities. These numbers are trending up as the national economy relies more on warehousing and e-commerce. In fact, non-fatal injuries have increased 33% since 2011 and fatalities have increased 20% in the same period. In 2019, a U.S business could expect an average cost of $42,000 per medically consulted injury and $1.22M for every fatality.
It’s not only loss of life, injury, and infrastructure damage that owners need to consider. Other less impactful scenarios can dent operational budgets. For example, driving forklifts over (or around) damaged concrete or expansion joints means replacing worn out tires more often than needed due to uneven surface transitions, overheating, and hard braking.
Data from forklift dealers shows that 40% of their maintenance is performed on tires. Of that number, 50% of those tire repairs or replacements come from driving over bad concrete and especially bad expansion joints in warehouses. So, by extension, 20% of all forklift maintenance is driven by bad concrete or bad expansion joints on warehouse floors.
Let that sink in for a minute.
If your business operates 8 hours a day, filling a few orders here and there, with one forklift, these statistics won’t move the needle on your operating costs. However, if you’re operating multiple shifts, perhaps around the clock, with a fleet of forklifts, then forklift maintenance eats into your gross margins on a daily basis.
Remember:
- The best ability is availability: assets taken out of service require replacements on your warehouse floor to ensure you can meet demand reliably.
- Timing is everything: you get to choose when to do preventative maintenance, but corrective maintenance chooses for you. The timing is never convenient.
- More is less: repair or replacement costs eat away at profitability.
- Insurance? What insurance? Tires lost under these conditions will not be eligible for warranty by service providers.
- The tab adds up fast; a set of tires can cost a business, on average, between $1,300 to $2,000, depending on the conditions and the market. Plus, factor in the loss of that asset for at least a day. In larger operations, this adds up and forces owners to purchase more forklift capacity to compensate for out-of-service forklifts.
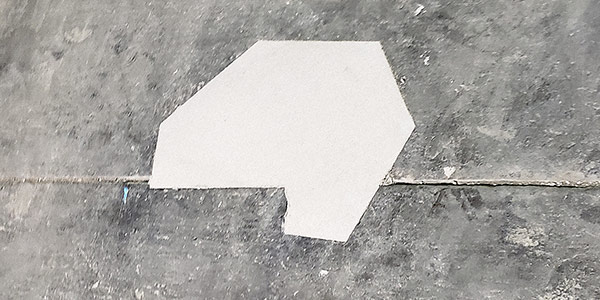
SOLUTIONS: What can owners do to fix these problems?
1. Take care of your concrete, it will take care of you.
Forklift tires are just the tip of the cost iceberg. Spalled, cracked, or damaged concrete can be caused by a host of issues (read our “Why Concrete Fails”), some of which don’t occur in the warehousing of dry goods. The most common causal factors can mainly be found in facilities with exposure to the elements, harsh chemicals, salts, or other process vessels that can start or accelerate damage. Setting up your facility with the proper containments (including protective or sacrificial coatings in some cases) and trenching for waste or condensation runoff may help prevent problems.
Physical damage to concrete is harder to prevent, but proactively maintaining the elastomeric gap in expansion joints can help, as can replacing them with epoxy-lined joints that reduce or eliminate the gap while maintaining flexibility. Simply lining an expansion joint with caulk once and then not touching it again for years does not work. Caulk or similar products must be replaced with regularity to counter the impacts of drying, cracking, and flexing.
If your concrete is already damaged, find the right professionals to fix it regularly. For high tempo operations, replacing with new concrete is not usually operationally feasible given the time needed to cut out damaged concrete and re-pour new. Epoxy repairs can help here, as they will adhere to the existing substrate well and can cure quickly once applied on damaged areas.
2. Back to that fast-moving and dangerous warehouse “highway”
If you have forklifts and pedestrian traffic moving in the same area, and your forklifts move at higher speeds, mitigate risk by segregating your traffic flow. Consider physical barriers like guardrails as tape on the floor doesn’t really cut it – people ignore these fictitious boundaries and they don’t set visual limits for drivers or pedestrians. Barriers will keep your operators in a permanent traffic flow and help prevent big maneuvers to avoid concrete problems. Think of a two-way highway separated by painted double traffic lines versus one with jersey barriers in the middle: which is safer?
The BIG Takewaway
We presented a lot of information. Here are your top takeaways:
- “Do nothing” is not an option when it comes to operating safely and efficiently, nor does it protect your margins.
- In 2019, a U.S business could expect an average cost of $42,000 per medically consulted injury and $1.22M for every fatality.
- 20% of all forklift maintenance is caused by bad concrete and expansion joints.
- Minor problems today turn into major ones tomorrow and fixing them preventatively does not cost much relative to the operational penalties and liabilities they pose. In other words, don’t swerve (like the forklift) to avoid problems that are easily fixable, allowing them to worsen around you will likely lead to a failure or major expense.
Banks Industrial Group specializes in the preventative maintenance and corrective repairs your facility needs to operate safely and efficiently. If the problems mentioned here are plaguing your business, contact us today.
You may also like our ice rink concrete floor repair case study.