
Containment Coatings and Repair Services
Banks Industrial Group (BIG) specializes in providing advanced containment coating and repair services for secondary containment areas, which are critical in safeguarding against chemical exposure, deterioration, and settlement cracking. Our company excels in repairing or replacing damaged concrete substrates and applying chemical-resistant coating systems to prevent corrosion and other types of damage.
Belzona Flexible Barrier 4361 application demo.
Need Containment Coating Work?
Request an estimate or consultation.
Benefits of BIG’s Containment Coatings and Repair Services
Environmental Protection
Our containment coatings and repair services offer excellent resistance to a wide range of chemicals, protecting your local environment from chemical spills, leaks, and contamination. By applying chemical-resistant coatings, we ensure that your secondary containment areas remain intact and functional, mitigating the risk of environmental damage.
Extended Service Life
We significantly extend the service life of secondary containment systems, sumps, pits, channels, and bases by utilizing high-performance coatings. Our epoxy coating options are designed to withstand harsh conditions, ensuring long-term durability and reducing the need for frequent repairs.
Avoid Reconstruction Costs
Our expert services help you avoid costly reconstruction by effectively restoring damaged concrete. We provide comprehensive solutions including resurfacing, crack repair, and expansion joint sealing, utilizing specialized acid-resistant epoxy to address specific chemical threats.
Reduced Downtime
BIG’s coatings and repair services are designed to minimize downtime with cold-applied, fast-curing materials. Our epoxy coatings are particularly effective in rapid application scenarios, ensuring that maintenance is carried out efficiently with minimal disruption.
Lower Maintenance Costs
Our long-lasting epoxy and urethane protective coatings dramatically reduce maintenance costs. By applying acid-resistant concrete coatings and chemical-resistant coatings for concrete, we enhance the longevity of your containment systems and decrease the frequency of maintenance interventions.
Chemical Exposure Protection
Our coatings offer superior protection against chemical exposure, including hydrochloric acid and sulfuric acid. Whether you need an acid-resistant concrete coating or a comprehensive chemical-resistant coating system, our solutions are engineered to withstand damaging acid and caustic chemicals.
Disbondment Prevention
Our coating products provide excellent adhesion and flexibility, bridging cracks and preventing disbondment. This ensures that the coatings remain securely in place and continue to protect the underlying concrete.
Impacts and Abrasion Protection
BIG’s coatings are formulated to offer exceptional compressive strength and resistance to impacts and abrasion. Our concrete epoxy coatings and acid-resistant epoxy coatings are ideal for environments subject to mechanical wear and tear.
Safe Application
We use cold-curing, solvent-free, no-VOC materials for our coatings, ensuring a safe application process with minimal environmental impact. Our approach aligns with best practices for safe and sustainable coating application.
Problem: Secondary Containment Area Deterioration Increases the Risk of Environmental Contamination
Secondary containment areas are crucial for preventing chemical spills from contaminating groundwater and the environment. These areas are susceptible to deterioration due to chemical exposure, settlement cracking, freeze/thaw cycles, and impact damage. In the event of an accident, such disrepair can compromise protection and lead to significant environmental contamination.
Owners must assess the extent of damage to the underlying substrate caused by wear, chemical exposure, or cracking. In severe cases, complete replacement of the concrete may be necessary. It is essential to consult a coatings expert to determine the most appropriate coating for protecting the concrete within the containment area from chemical spills and splashes.
Regulations at federal, state, and local levels mandate the proper maintenance of secondary containment areas. Failure to comply can result in fines, and the cleanup and legal costs associated with hazardous material leaks can be substantial.
Solution: Rebuild or Replace Damaged Concrete and Protect It with an Appropriate Coating
Owners should thoroughly evaluate, repair, or replace the underlying substrate based on the extent of damage. They need to assess whether the substrate can support a coating suitable for the chemical risks involved.
Belzona epoxies, including specialized urethane formulations, are proven to be effective for secondary containment repair and protection. These chemical-resistant coatings are engineered to provide excellent resistance to harsh industrial environments. Depending on the chemicals involved, we can match the appropriate coating to ensure optimal performance.
Our repair mortars and protective coatings are designed to be safe, solvent-free, cold-applied, fast-curing, and offer strong bonding. We apply them quickly, minimizing downtime and ensuring long-term protection. Our containment coatings and repair services offer peace of mind by addressing both legal and environmental risks.
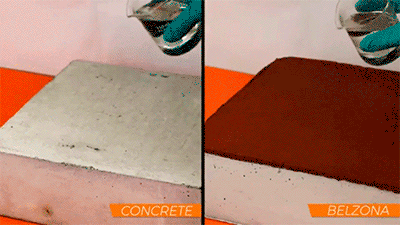
HCl acid test: concrete on left is damaged, Belzona coating on right shields the concrete from acid attack.
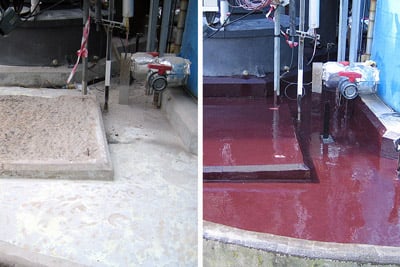
Before and after of concrete repair and containment coating.
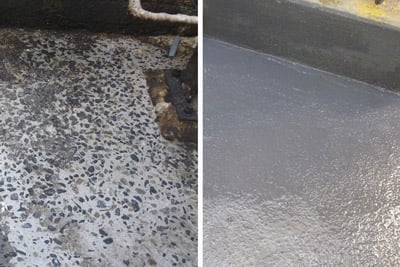
Deteriorated concrete is repaired and protected.
Industry-Leading Containment Coatings and Repair Services
At Banks Industrial Group, we use high-quality Belzona epoxy repair mortars repair mortars to patch and rebuild damaged containment walls, floors, bases, and sumps. These materials provide excellent compressive strength, impact resistance, and durable adhesion to concrete. We offer specialized formulations to withstand extreme chemical exposure, including acid-resistant and sulfuric acid-resistant coatings tailored to your needs.
Additionally, we apply advanced Belzona protective coatings to protect existing and newly constructed containment areas. We offer a range of high-performance formulations that can tolerate mild, dilute, or concentrated chemicals, even under high temperatures and concentrations. Our coatings’ strong bonding characteristics prevent delamination and ensure reliable protection over existing coatings.
To achieve the best long-term protection, we carefully select and match the right containment coating with your specific operating conditions. By using the appropriate coating, we minimize the need for frequent repairs and ensure that your containment structure is well-protected. We provide expert consultation and site evaluation to identify the best materials for your operational environment.
For more information on secondary spill containment, check out our blog post, "Spilling the Facts on Secondary Spill Containment," to understand when, why, and how secondary spill containment should be an integral part of your operational safety protocol.
Banks Industrial Group specializes in containment coatings and repair services, above-ground storage tank insulation, protective coatings, concrete, and related maintenance and repair services. Our innovative and cost-saving solutions help keep your facility running efficiently. For more information about our concrete floor repair and other industrial solutions, contact our team today by calling 856-687-2227.