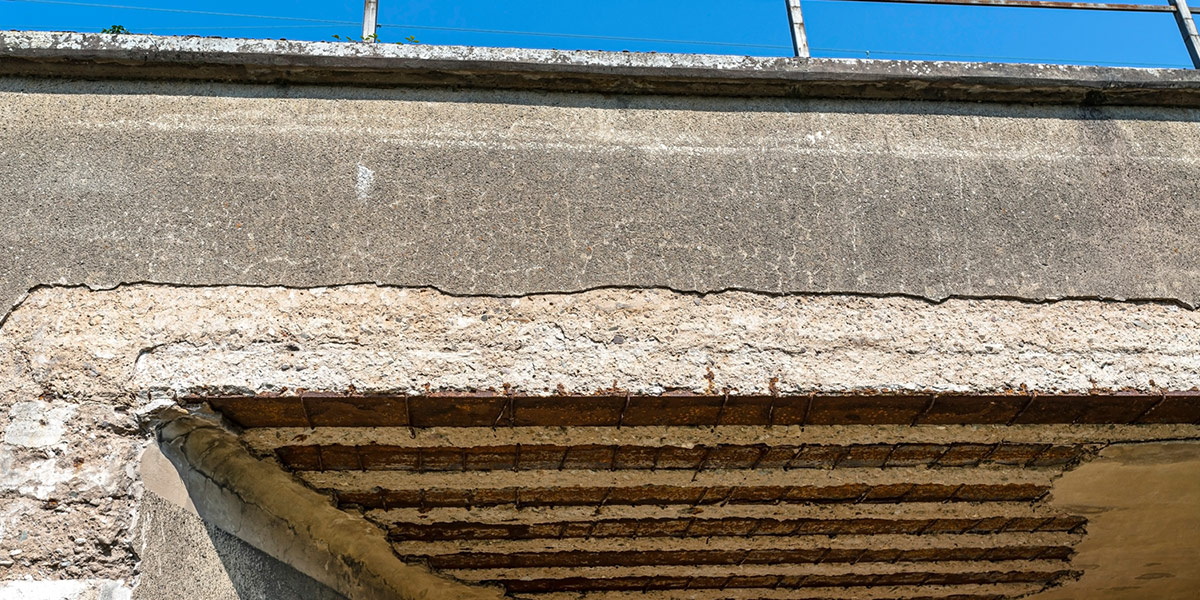
Contents
If concrete is strong enough to hold up tall buildings, support landing planes, and create sea walls against the ocean, how can it fail after years of rock-steady service?
If you are a mechanical, chemical, or structural engineer, you already know the answer to that question.
For the rest of us without those advanced degrees, this article should help you understand why the concrete in your facility is changing, degrading, and possibly failing
We want to simplify this to the maximum extent possible, so any chemical, mechanical, or structural engineers reading this should look elsewhere for equations or calculations.
To understand why concrete fails, let’s examine its basic composition:
- Concrete = cement + aggregate + water + chemical mixtures + additives + air. (Aggregate, usually some form of crushed rocks or minerals, can change over time as it reacts chemically with the elements and intrusions into concrete.)
- Concrete is porous; moisture, liquids, chemicals, and air can and will penetrate and permeate it. It’s not if, but when.
- Concrete has a high pH; this is because concrete is alkaline when created, which means the opposite of acidic. This, like aggregate, can change over time as concrete interacts with other chemicals and materials.
- Concrete must properly cure; it takes four weeks in order to achieve full strength.
- Concrete has high compressive strength (ability to resist heavy loads), but a lower tensile strength (ability to pull apart). To increase tensile strength, you must add steel.
- Concrete expands and contracts in reaction to temperature changes.
Simply put, making concrete is like your grandmother’s homemade spaghetti sauce – it may be one recipe, but no two batches come out exactly alike. Each batch comes with varying qualities based on the intended use and skill of the producer. With concrete, how it was mixed, cured, and transported all play a role in its longevity.
Why Concrete Fails
- Imperfections—faulty design, composition, or installation
- Damage—a one-time or recurring event that harms the product
- Deterioration–the natural lifecycle of concrete, we all get old!
In many ways, we can compare concrete to our own personal health. We are not born with the same genetics, we don’t always take care of ourselves the way we should, and sometimes we get into accidents.
Let’s discuss each of these elements in brief.
Imperfections
Concrete imperfections can be summed up in three ways:
- Someone designed it that way or maybe misapplied a design
- The materials used may not be optimum or were not added in the right proportions for the task
- The contractor installing it made mistakes or took shortcuts
Remember your grandmother’s spaghetti sauce? Maybe she mixes one batch a little spicier and maybe the next a little sweeter. The ingredients might be the same, but the proportions change. Concrete is no different. Concretes can be mixed differently to produce different qualities, such as strength, for example. High-end concrete used to protect underground military bunkers, support heavy bridges, or surround nuclear power plants exceeds the strength requirements for the concrete on sidewalks or driveways.
If Grandma is sipping her wine while she creates her sauce, maybe she gets a little tipsy and goes heavy with one ingredient, or perhaps she takes a shortcut by using the microwave or food processor to quicken certain steps. Contractors putting down concrete can make the same mistakes or sometimes get forced into mistakes by weather, construction schedule changes, etc. A miscalculation such as removing supporting forms too early can cause deformation or damage.
Pro tip for readers: you may blame your concrete engineer, manufacturer, or contractor for your concrete results, but never blame Grandma for how the sauce turned out. Remember, she made it with love, it’s always delicious.
Damage
No need to belabor the concept of damage because we all know…stuff happens. Concrete is a reliable product with great properties that make it hard to beat. However, the following can accelerate its failure:
- Overloading it (over time or instantaneously)
- Chemical spills
- Natural and man-made disasters (namely, earthquakes and fire)
To drill down further:
Overloading:
- Too much of a moving load (for example, a heavy car or truck rolling over a concrete bridge).
- Too much of a live (continuous) load (for example, too much weight parked in a concrete parking structure).
- High impact load (like a car hitting a column at full speed).
- These loads create compressive, tensile, or shear stresses and when repeated over time, or even one time, they can cause failure.
Chemical damage:
- Solid chemicals won’t attack concrete. Chemicals must be in solution form (above certain concentrations) to successfully attack concrete.
- Acids can attack from multiple forms; in solution, runoff from acidic industrial wastes, sludges, fruit juices, animal wastes, or acid rain.
- Aluminum chloride, calcium bisulfite, hydrochloric acid (all concentrations), hydrofluoric acid (all concentrations), nitric acid (all concentrations), sulfuric acid (10-80%) and sulfurous acid. Containment of these seven chemicals requires extra protection.
It should be noted that concrete used to contain acid spills might be damaged if the vessel holding those acids leaks into the concrete. Remember the importance of balanced pH in concrete? It can change depending on the application of chemicals.
Earthquakes and fire:
- Fire exploits the temperature-driven expansion and contraction effect on concrete, breaking down its chemical composition causing volume changes, cracking, and disintegration.
- Any steel reinforcing the concrete also expands in the process, decreasing concrete’s tensile abilities.
- Do we need to explain earthquakes? Didn’t think so. Let’s move on.
Deterioration
In the race against time and concrete, time will always win. Why? Concrete’s porous nature can be permeated by water, salts, sulfates, chemicals, and air. This can (and will eventually) change its composition, create expansion, reduce tensile strength, and cause tiny cracks to form underneath the surface. Small cracks become large, visible cracks and the concrete eventually fails.
There’s a very good chance it will be due to one of the following:
- Corrosion
- Exposure to chemicals
- Alkali-aggregate reactions
- Sulfate attack
- Freeze thaw cycles
- Erosion/Abrasion
Corrosion:
- Steel is sometimes used to reinforce the concrete from within, adding to its tensile strength.
- When that metal is exposed to moisture, oxygen, and salts that permeate the concrete, it starts to corrode.
- This causes the metal to expand, create micro-fractures in the concrete, and eventually cracks form.
Chemicals:
- Same damaging impact as the moisture, oxygen, and salts.
- Additionally, chemicals break down the composition of the concrete, perhaps lowering the pH of the cured mix and causing disintegration.
- Chemicals can react with the aggregates, leading to possible expansion and fracturing.
- Chemical runoff from streams, oceans, or soil, notably sulfate-rich runoff, can penetrate concrete and (you guessed it) cause expansion, pressure, and deterioration.
- Runoff is typically found in places like chemical plants or certain industrial facilities, but can also be found in your driveway when you apply fertilizers or treatments to your lawn.
- Sulfate runoff issues are common in arid climates, like the southwest or the Northern Plains.
Freeze-thaw:
- Common in climates where there’s moisture and the potential for freezing temperatures.
- Moisture inside porous concrete can freeze and expand by 9%.
- In extreme weather climates, frozen roads doused in chemicals, salts, and snow, create a “perfect storm” to destroy existing concrete or other road surfaces.
- Regardless of climate, all concrete will expand and contract based on temperature, which will eventually cause damage of some kind.
Erosion and abrasion:
- When water runs over a surface, any surface roughness will cause tiny bubbles in the water to expand and collapse, a process called cavitation.
- These bubbles impact the surface of the concrete and slowly erode the surface. Abrasion can result from frictions, scrapes, etc. from wheeled traffic, steel, or hard rubber on floors found in warehouses or manufacturing plants.
Is YOUR concrete in danger of failing soon?
Know the signs of distress:
- Spalling or delamination
- Cracking
- Corrosion
- Wear
- Leakage
- Settlement
- Disintegration
- Scaling
While these distress signals may be obvious to most people, there are few terms that might require some explanation.
Spalling looks like parts of concrete have flaked off the main body. Signs of orange rust indicate the presence of corrosion. Settlement occurs when one slab or portion of concrete sinks further into the surface than an adjacent piece of concrete. This may cause cracking if the two pieces originally were one continuous piece. Finally, scaling looks like a lesser version of spalling, with thin layers of flaking occurring at the surface, without getting to the underlying aggregate.
The BIG Takeaway
In less than 1,500 words we have covered a lot. Your four key points are:
- Concrete, while durable and strong, changes over time.
- Moisture, chemicals, air, etc. can permeate concrete and accelerate those changes.
- Concrete, if not cared for, will degrade over time when exposed to elements.
- No two batches of concrete are ever exactly the same.
We will write future blog posts on how to protect your concrete and repair it. In the meantime, think BIG, stay safe and contact us if you have any questions.
You may also find our ice rink concrete floor repair case study of interest.
Sources:
Emmons, Peter. Concrete Repair and Maintenance Illustrated. RS Means, 1993.
Gambhir, M.L. Concrete Technology: Theory and Practice. McGraw Hill Education, 2013.
Kerkhoff, Beatrix. “Effects of Substances on Concrete and Guide to Protective Treatments” 2007. PDF file.
Portland Cement Association. “Types and Causes of Concrete Deterioration” 2002. PDF file.
ACI Committee 201. Guide to Durable Concrete. American Concrete Institute, 2016.